30.03.2020
Magnetic disc separator processes beach sands
Bunting Magnetics Europe, Berkhamsted, UK, has manufactured its latest magnetic disc separator (MDS) for processing and separating key minerals from a beach sands deposit. The three-stage unit is destined for a mineral processing operation in Africa.
It will enable an accurate separation of minerals with varied magnetic susceptibilities. Typically, an MDS features up to three high-intensity electromagnetic discs, each set at a different height from a feed conveyor. The first disc will be set the furthest from the feed material, in order to extract only the most magnetically susceptible particles. The second and third discs are set at lower gaps, increasing the magnetic force at each disc and therefore separating different grades of magnetic material. Magnetic intensity can also be further adjusted by varying the current of each coil to suit each client’s specific mineral separation requirements.
Unlike competitive designs, Bunting’s MDS has a designated coil for each magnetic disc. The coil and magnetic disc relationship allows precise adjustment of the magnetic field at each stage and ensures accurate generation of the optimum magnetic field.
In this latest project, the beach sands mineral mix includes ilmenite, garnet, monazite, silica sand, rutile, and zircon. Prior to determining the specification of the production-scale MDS, Bunting undertook comprehensive material tests in its mineral processing laboratory at Redditch. The controlled tests determined the magnetic power required at each stage to produce a successful separation.
The production-scale MDS has six distinct separation stages. In operation, the beach sands mineral mix is evenly fed via a vibratory feeder on to a conveyor belt which passes under all three magnetic discs. Each magnetic disc produces a different magnetic force to separate a specific group of minerals. In addition, each magnetic disc is positioned at a tilt of approximately 1 – 2mm to generate two slightly different magnetic fields at the front and rear of each disc. Subsequently, there are six separate stages of separation.
In this beach sands application, disc 1 is set to first produce 7000 gauss on the surface the belt (separation stage 1) and 8000 gauss at the rear (separation stage 2). The mineral mix is conveyed under the clockwise rotating disc with the 7000 gauss magnetic field removing larger iron-bearing particles including the highly paramagnetic ilmenite (FeTiO3) into the first collection area to the left of the feed direction. The black mineral rich fraction is used as a source for TiO2.
The magnetic field strength at the rear of the disc is 8000 gauss and removes any remaining and smaller-sized particles of ilmenite. The combined ilmenite recovery rate from disc 1 is +95%. www.buntingeurope.com
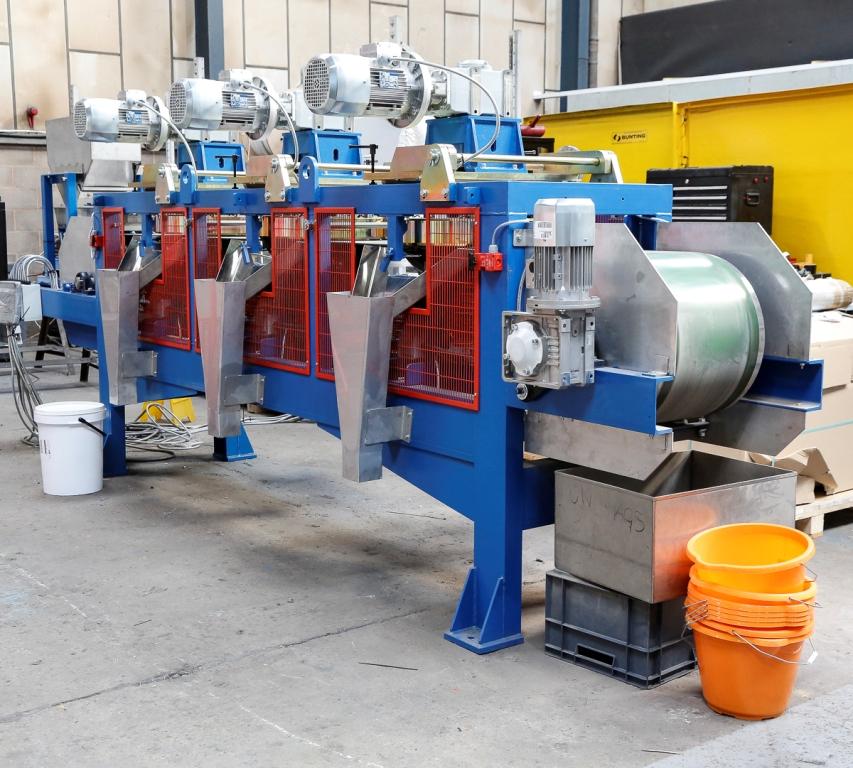
Bunting magnetic disc separator set up for final product tests
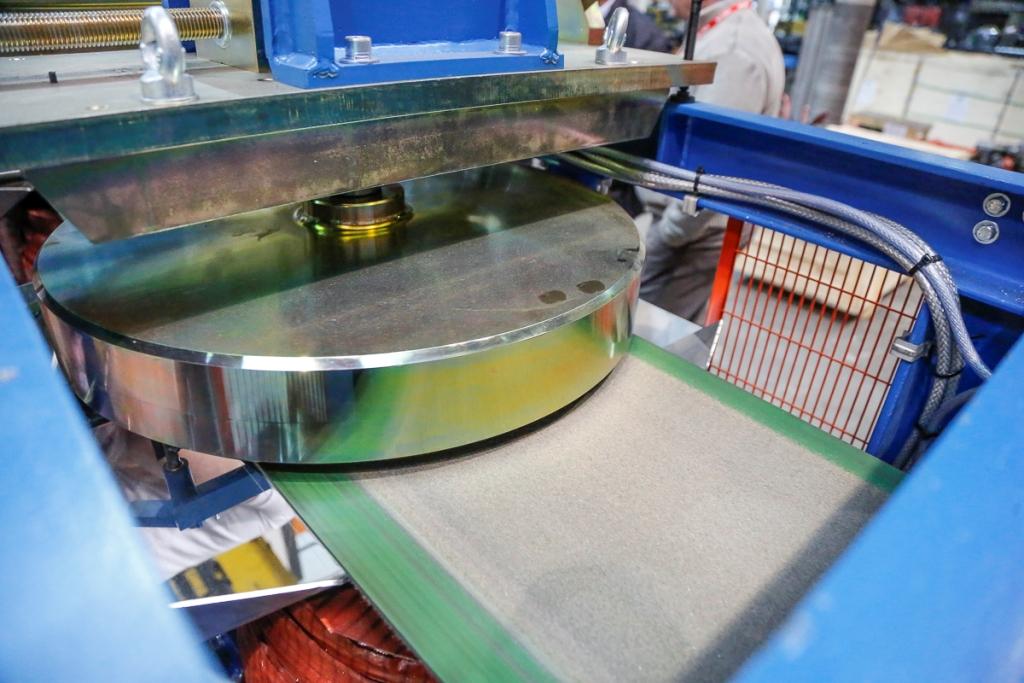
One of the three magnetic discs located above the conveyed mineral mix
« Back
|