05.02.2024
When every drop counts
How fragrance manufacturer LUZI uses mixing and dispersion technologies
Swiss fragrance manufacturer LUZI develops and produces essences and fragrances for a number of application areas, from interior maintenance and cosmetics to fine fragrances.
The fragrance products are accompanied by special requirements in the production process: In addition to a very high homogeneity of the produced solutions, what is important for the medium-sized company in its day-to-day production activities is - above all - a complete discharge of the product’s residual quantities at the end of a batch, easy and resource-saving cleanability of systems as well as efficient and complete drying. For wetting, dispersing and mixing, LUZI exclusively uses technologies from the mixing technology specialist ystral.
LUZI has two production sites - in Switzerland and Malaysia - with an annual capacity of 8,000 tons in total. At its headquarters in Dietlikon, Switzerland, LUZI uses a 3- and 5-ton process system from ystral for the induction, wetting and dispersing or solving of powder components such as vanillin and liquid components such as orange oil in the main liquid component dipropylene glycol (DPG).
For both systems, a powder wetting and dispersing machine ystral Conti-TDS, which is installed outside of the vessel, is connected to a process vessel via pipes, in which an ystral Jetstream Mixer is installed.
For the production of premixed solutions, as well as the mixing of small casks up to approx. 1,000 kg, LUZI also uses a total of 12 ystral multipurpose systems with their own movable vessel. Another ystral system can be found at the production site of LUZI in Malaysia.
“We have successively expanded our inventory of ystral systems and plants at both of our locations, and are now realising our complete production with technologies from ystral”, says Thomas Danuser, Head of Production at LUZI.
High homogeneity required
A central demand in production is placed by LUZI on very high homogeneity of the produced solutions. Technologies from ystral can meet these demands: Using the vacuum expansion method, the ystral Conti-TDS disperser achieves complete deagglomeration and wetting of the powder particles in a matter of microseconds.
The air contained in the powder is expanded by a multiple through an induction vacuum, which significantly enlarges the distance between the particles. The powder particles have the largest possible distance to each other in the dispersing zone, and can thus be fully wetted and dispersed individually. This prevents agglomerates.
The air contained in the powder is separated from the significantly heavier dispersion through the centrifugal effect of the fast-running rotor and coalesces to large air bubbles. These are then pumped to the process vessel with the liquid flow, where they can easily escape. Once powder induction is complete, the powder inlet is closed. The intensive shearing via rotor and stator in this phase supports deagglomeration.
At the same time, a permanent homogeneous mixing occurs in the vessel via the ystral Jetstream Mixer. Jetstream mixers combine a turbulent micro mixing zone in their mixing head with a vertical macro-mixing of the entire vessel content. Other than when using a conventional agitator, the product is actually fully mixed homogeneously at the end of the mixing process – without any unmixed zones and sediments – and consistent results are achieved independent of the batch size and the fill level in the vessel.
Residue draining
For the flavour solutions that are produced on the process systems to be used fully, ystral has attached a complete discharge nozzle at the respective lowest point, below the disperser, with which the operator can collect the residual quantity of the product remaining in the system by means of a hand valve.
To enable this manual residual drainage, the process systems at LUZI’s premises are positioned slightly higher than is the case with other ystral systems.
High dosing accuracy
The solutions produced are filled into different casks at LUZI, with a size between 25 and 1,000 l.
For the fragrance products to be dosed as accurately as possible into the respective cask, and for the process to be user friendly at the same time, a pendant control panel is used. This can be used by the employee to control the speed and thus the throughput of the Conti-TDS, whose pumping performance is used for the product discharge.
Shortly before reaching the target volume, the speed of the Conti-TDS is reduced by the operator and small doses are added until the platform scale shows the target value of the respective cask.
Water- and energy-saving cleaning
Another central requirement of LUZI placed on the process systems used is good and fast cleanability. ystral machines and systems follow the rules of hygienic design, and are thus designed in a way that enables easy and complete cleanability – without gaps, threads or hidden zones. Even areas such as the underside of a mixer flange can be cleaned without shadows by means of special cleaning heads. The ystral Conti-TDS disperser is used here as CIP pump for circulation of the cleaning medium. Therefore, a separate pump is not required for cleaning.
Furthermore, it is very important for the fragrance manufacturer that cleaning processes can be implemented energy-efficiently and by using as little cleaning water as possible. Therefore, ystral integrated a flush water tank between the two process systems at the Dietlikon site with a capacity of 600 l, which is used jointly by both systems. The approx. 60 °C hot water from this tank is used for a pre-rinsing step via several spray heads positioned in the vessel, pumped out, and the system is then thoroughly cleaned in a second rinsing step using 80 °C hot water, which is in turn used in the next cleaning process for pre-cleaning. This way, LUZI can significantly reduce the water and energy requirement during cleaning.
Complete drying
What was also important for the fragrance manufacturer with regard to the system design was that the system can be fully dried following hot water cleaning within a short time, to rule out a falsification of the following batch by the cleaning medium. For drying, the system is subjected to an air blast for several minutes. This blow-out process was further optimised for the latest ystral system that was installed in 2022, compared to the other two ystral systems, and is defined in the control as separate process step with the respective switching sequences of the individual valves.
By controlling different spray heads, the cleaning medium residues remaining in the system are blown out from top to bottom using compressed air. Thanks to their hygiene design, the ystral systems can be dried automatically after only about 10 minutes using three cleaning cycles, and manual drying of the last remaining water drops is still only required on the manhole covers.
“The individual solutions for the discharge of residual quantities, a water- and energy-saving cleaning or fast drying of the system using compressed air demonstrate how precisely ystral has tailored the design of the three process systems to our requirements”, says LUZI Production Manager Danuser. “We value this high customer focus and the willingness of ystral to develop solutions together with the user for their specific requirements.”
www.ystral.com
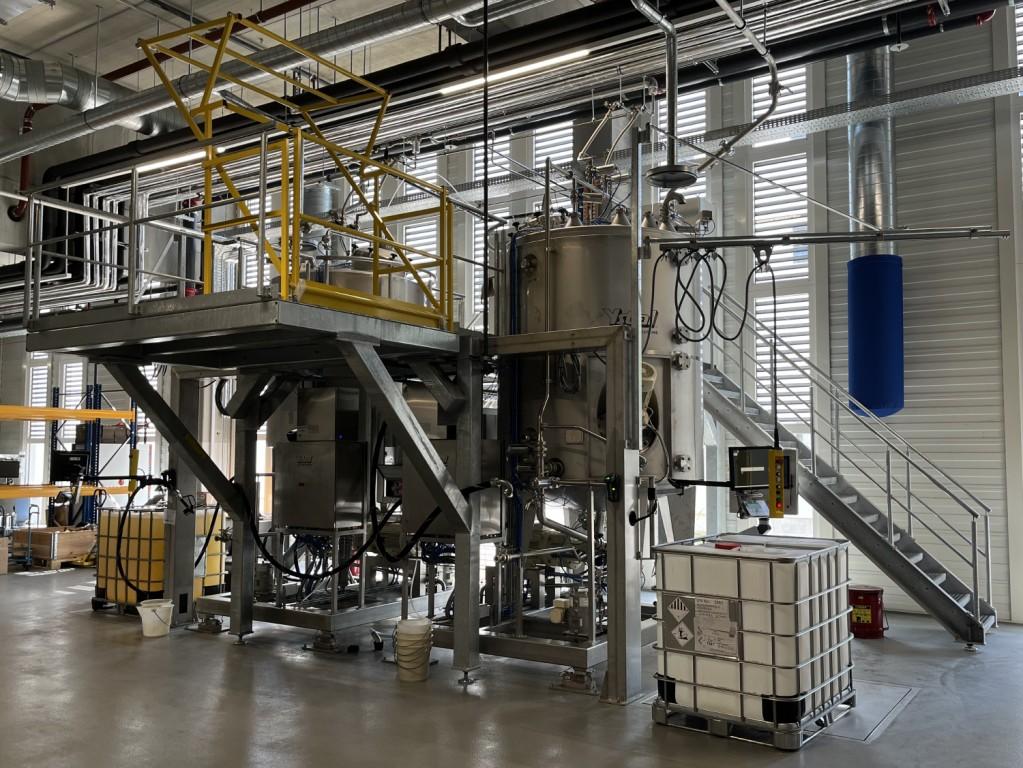
(Top) The fragrance manufacturer LUZI uses a 3- and a 5-ton process system from ystral for the production of flavour solutions at its headquarters in Dietlikon, Switzerland. The dimensions of the two redundantly operating systems including platform are 8.5 m x 6.9 m x 4.4 m
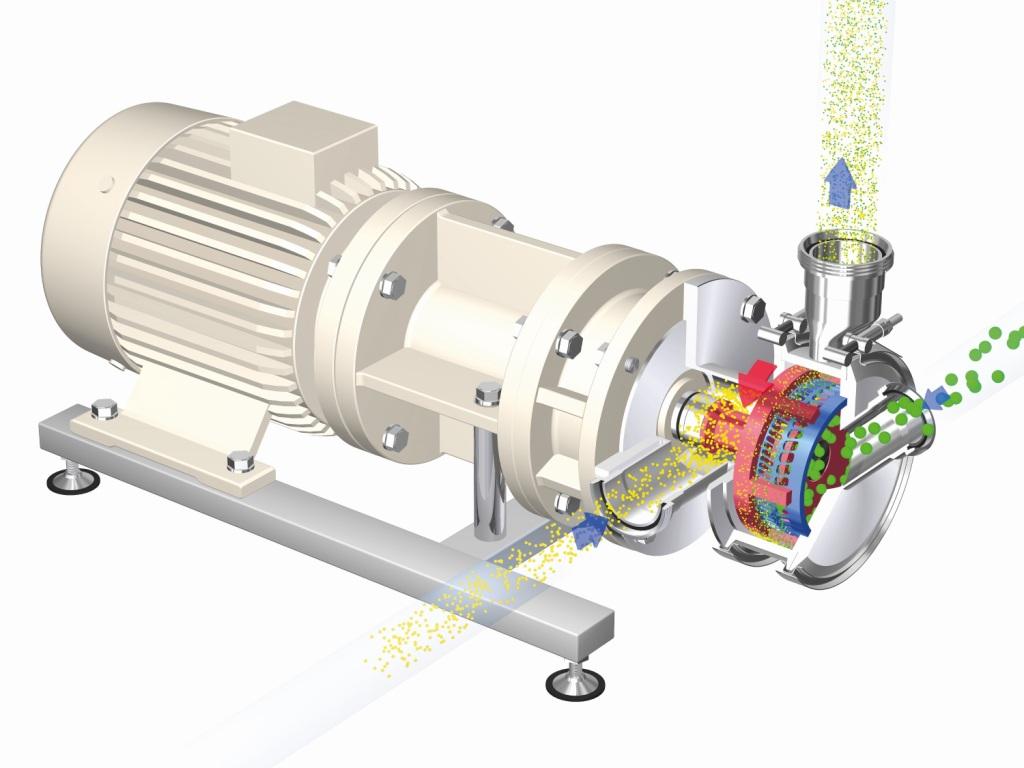
(Middle) The powder wetting and dispersing machine ystral Conti-TDS. Using the vacuum expansion method, the disperser achieves complete deagglomeration and wetting of the powder particles in a matter of microseconds
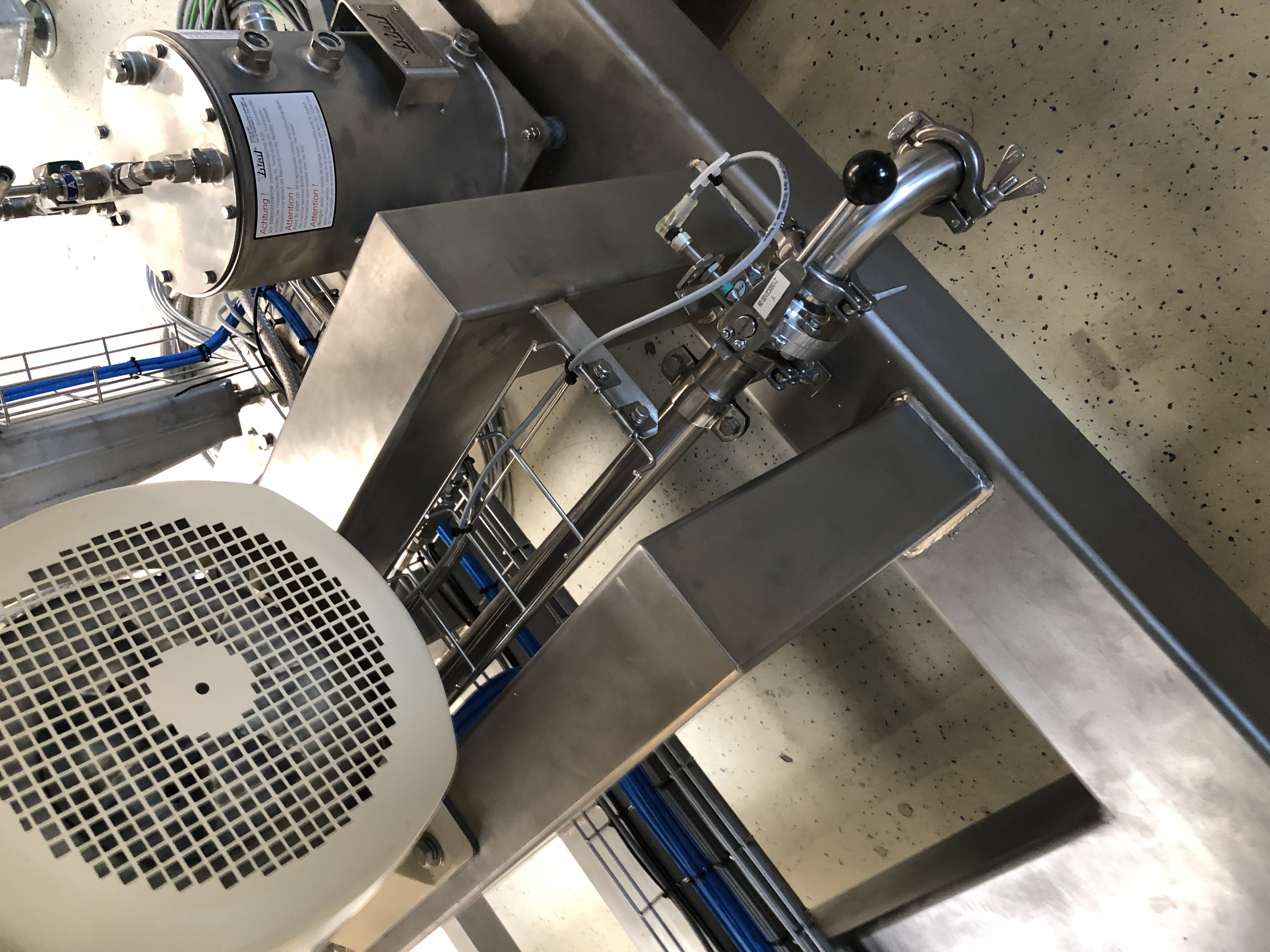
(Bottom) Other than when using a conventional agitator, the product is actually fully mixed homogeneously at the end of the mixing process when using the ystral Jetstream Mixer – without any unmixed zones and sediments – and consistent results are achieved independent of the batch size and the fill level in the vessel (photo credit: ystral).
« Back
|